Building an agricultural repair shop in Fargo, ND, requires careful planning and consideration of the region’s unique challenges.
From navigating local building codes to managing temperature control in extreme weather conditions, farmers must make informed decisions to ensure their repair shop is functional, efficient, and compliant.
This guide will help you understand the key factors involved in agricultural repair shop construction in Fargo, ND.
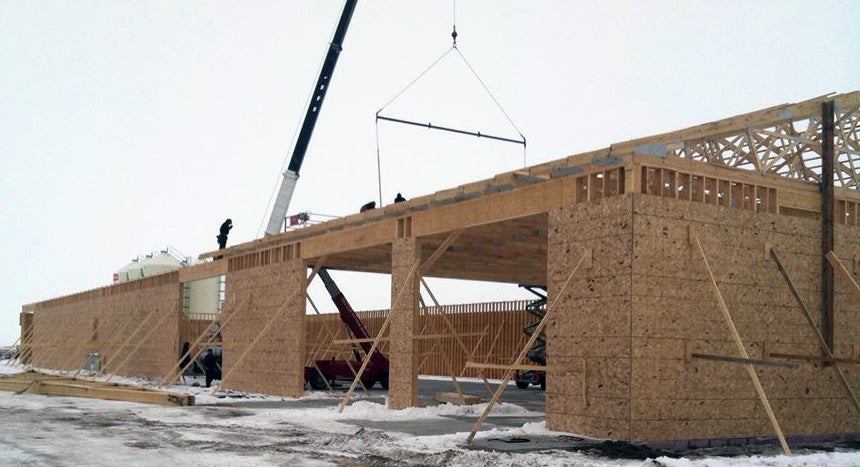
1. Understanding Agricultural Building Codes in Fargo A Guide to Finding the Right Contractor
One of the most critical aspects of agricultural repair shop construction is ensuring compliance with local building codes.
In Fargo, it’s essential to work with contractors who have experience in the agricultural sector and a deep understanding of the specific regulations that apply to these structures.
To find the right contractor for your project, consider the following tips:
- Look for contractors with a proven track record of successful agricultural construction projects in the Fargo area.
- Check references and review past projects to gauge their experience and quality of work.
- Verify that they are licensed, insured, and familiar with the latest agricultural building codes and regulations.
- Consult local trade associations or agricultural agencies for recommendations on reputable contractors in Fargo.
Resource | Benefit |
---|---|
North Dakota Farmers Union | Connects farmers with experienced contractors |
Fargo Building Inspections Department | Provides information on local building codes |
North Dakota Association of Builders | Offers a directory of licensed contractors |
2. Temperature Control in Agricultural Repair Shops Managing North Dakota’s Extreme Climate
Fargo’s harsh winters and hot summers pose unique challenges for temperature control in agricultural repair shops.
To ensure your shop remains functional and comfortable for workers year-round, consider the following strategies:
- Invest in a high-efficiency heating and cooling system designed to handle extreme temperatures.
- Ensure proper insulation and weatherization to minimize heat loss in winter and heat gain in summer.
- Install a programmable thermostat to maintain optimal temperatures and reduce energy waste.
- Consider energy-efficient options like radiant floor heating or geothermal systems to reduce operational costs.
System Type | Advantages | Considerations |
---|---|---|
Forced Air Heating/Cooling | Fast temperature adjustments, easy installation | May have uneven heat distribution |
Radiant Floor Heating | Even heat distribution, energy-efficient | Higher installation costs, slower to adjust |
Geothermal Heat Pumps | Energy-efficient, eco-friendly, long lifespan | High upfront costs, requires land for installation |
3. Determine the Optimal Shop Size for Your Agricultural Repair Needs
When planning your agricultural repair shop construction, it’s crucial to determine the right size to accommodate your current and future needs.
Consider the following factors:
- Types and sizes of equipment you need to repair and store
- Space requirements for work areas, storage, and office facilities
- Anticipated future growth of your farming operation
- Local zoning regulations and setback requirements
To ensure you have enough space for large farming equipment, follow these steps:
- Measure the dimensions of your largest equipment, including height, width, and length.
- Add extra space around each piece of equipment for comfortable maneuvering and repairs.
- Include additional room for storage, workbenches, and other necessary features.
- Consider adding a mezzanine or second floor for office space or additional storage.
Avoid common mistakes like underestimating equipment sizes, neglecting to account for future growth, or failing to consider local zoning regulations that may limit the size of your shop.
4. Overcoming Construction Challenges in Fargo’s Harsh Weather Conditions
Fargo’s extreme weather, including frigid temperatures, heavy snowfall, and frost, can pose significant challenges during the construction process.
To mitigate these issues, consider the following strategies:
Challenge | Solution | Benefit |
---|---|---|
Frozen ground | Use ground thawing equipment | Enables excavation and foundation work |
Snow and ice accumulation | Install a temporary shelter or heating system | Protects workers and materials, prevents delays |
Cold temperatures | Choose cold-resistant materials and insulation | Ensures durability and energy efficiency |
Additionally, work with your contractor to develop a construction timeline that takes into account potential weather-related delays and prioritizes critical tasks during the most favorable conditions.
5. The Importance of Agricultural-Specific Building Codes in Your Repair Shop’s Design
Agricultural building codes are designed to address the unique safety, durability, and operational requirements of farm structures.
In Fargo, key regulations that may impact your repair shop’s construction include:
- Structural requirements for heavy equipment loads
- Ventilation and air quality standards for worker safety
- Electrical and plumbing codes specific to agricultural facilities
- Environmental regulations for waste management and runoff control
To ensure compliance and avoid costly mistakes, work closely with your contractor and local building officials to:
- Review and understand the applicable agricultural building codes
- Obtain necessary permits and schedule required inspections
- Incorporate code-compliant features into your shop’s design
- Maintain detailed records of your construction process and compliance measures
Why Agricultural Repair Shop Construction in Fargo Matters
Investing in a well-designed, code-compliant agricultural repair shop is essential for the long-term success and efficiency of your farming operation in Fargo, ND.
By understanding the unique challenges posed by the region’s climate, building codes, and construction requirements, you can create a facility that:
- Provides a safe, comfortable, and productive work environment for your employees
- Accommodates your current and future equipment repair and storage needs
- Operates efficiently and sustainably, reducing energy costs and environmental impact
- Complies with local regulations, minimizing legal and financial risks
Furthermore, a well-constructed agricultural repair shop can add significant value to your farm, serving as a valuable asset for generations to come.
By prioritizing careful planning, collaborating with experienced professionals, and investing in quality materials and systems, you can ensure that your agricultural repair shop construction project in Fargo, ND, is a success.
Embrace the opportunity to create a facility that not only meets your immediate needs but also positions your farm for long-term growth and resilience.
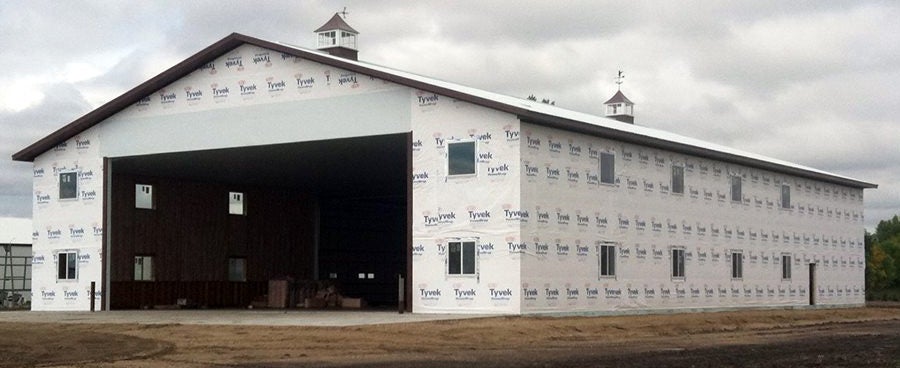
FAQs
How can I find contractors in Fargo who are familiar with agricultural building codes?
To find contractors with agricultural building code expertise, check with local trade associations, such as the North Dakota Farmers Union or the North Dakota Association of Builders. You can also consult the Fargo Building Inspections Department for recommendations and resources.
What are the best practices for managing temperature control systems in an agricultural repair shop in North Dakota?
Best practices include investing in high-efficiency heating and cooling systems, ensuring proper insulation and weatherization, using programmable thermostats, and considering energy-efficient options like radiant floor heating or geothermal systems. Work with your contractor to choose the best system for your specific needs and budget.
How do I determine the ideal size for an agricultural repair shop in Fargo to accommodate large farming equipment?
To determine the ideal shop size, measure the dimensions of your largest equipment and add extra space for maneuvering and repairs. Include additional room for storage, workbenches, and other necessary features. Consider future growth and local zoning regulations when making your final decision.
What are the typical challenges involved in constructing a repair shop in Fargo’s extreme weather conditions?
Typical challenges include frozen ground, snow and ice accumulation, and cold temperatures. Solutions involve using ground thawing equipment, installing temporary shelters or heating systems, and choosing cold-resistant materials and insulation. Work with your contractor to develop a weather-contingent construction timeline.
How do agricultural-specific building codes in Fargo impact the design and construction of repair shops?
Agricultural building codes address safety, durability, and operational requirements specific to farm structures. Key areas of impact include structural requirements for heavy equipment loads, ventilation and air quality standards, electrical and plumbing codes, and environmental regulations. Ensure compliance by working closely with your contractor and local building officials.